Weld Distortion Management
The process of estimating distortion effects on the structural components of a ship can be complex and lead to excess material waste or rework. The Weld Distortion Management solution was developed to improve and automate these tasks.
Shrinkage occurs in more or less all metal-work related processes involving thermal processes. It causes distortion, requiring excess material and leading to inaccurate final dimensions. Compensating distortion can cause major efforts for rework, reportedly up to hundreds of $/ton depending on ship type and complexity.
Weld Distortion Management offers a suite of applications that allow shipyards to apply unique methods for advanced distortion control to their steel and metals production processes.
It utilizes quality control data such as measuring data commonly acquired today by using devices and combines this information with a rule base created from shipyard experience and heuristics. It is therefore a powerful addition to existing quality control tools in use.
Concept
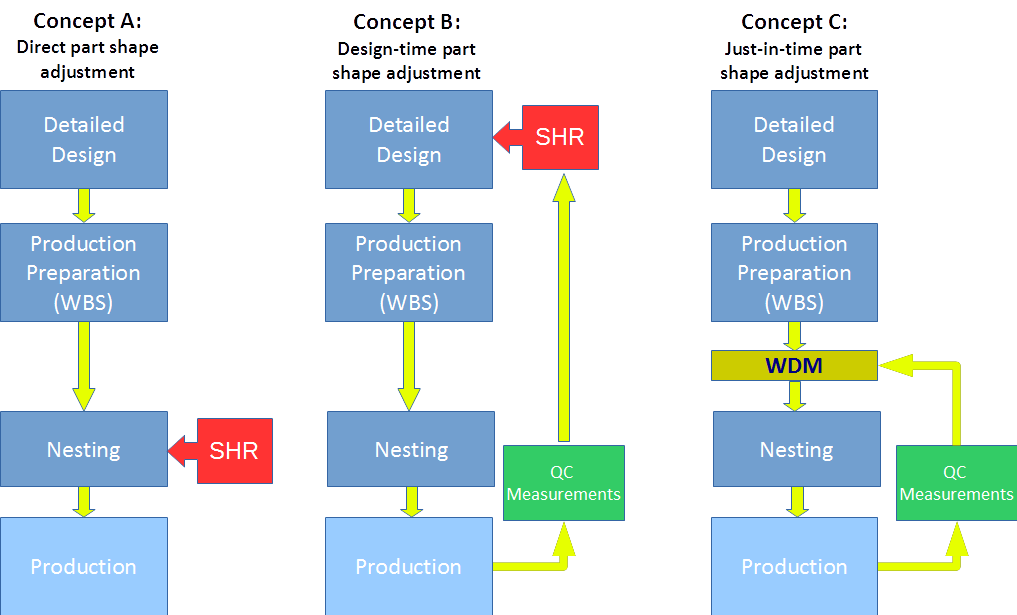
To reduce and control distortion, conventional approaches (beyond pure experience based methods) involve slow feedback cycles based on observed production effects which are used to either modify part-level geometry definition or to apply shape corrections based on heuristics. In these concepts, usually static factors and fixed instructions are applied for geometric modification of part shapes.
In WDM, similar information is used. It is, however, applied in an incremental method that substantially reduces the feedback time and therefore allows to take the actual production process technologies and the production sequence into consideration. This way, corrective actions can be applied just-in-time shortly before part production, without mandating design changes.
Using WDM, the actually planned production sequence is considered as well as the capabilities of the production environment based on a facility model are taken into account. The description includes characteristics of the different work places or work stations and how they are used during the production of various categories of parts, assemblies, sections, modules, blocks etc.
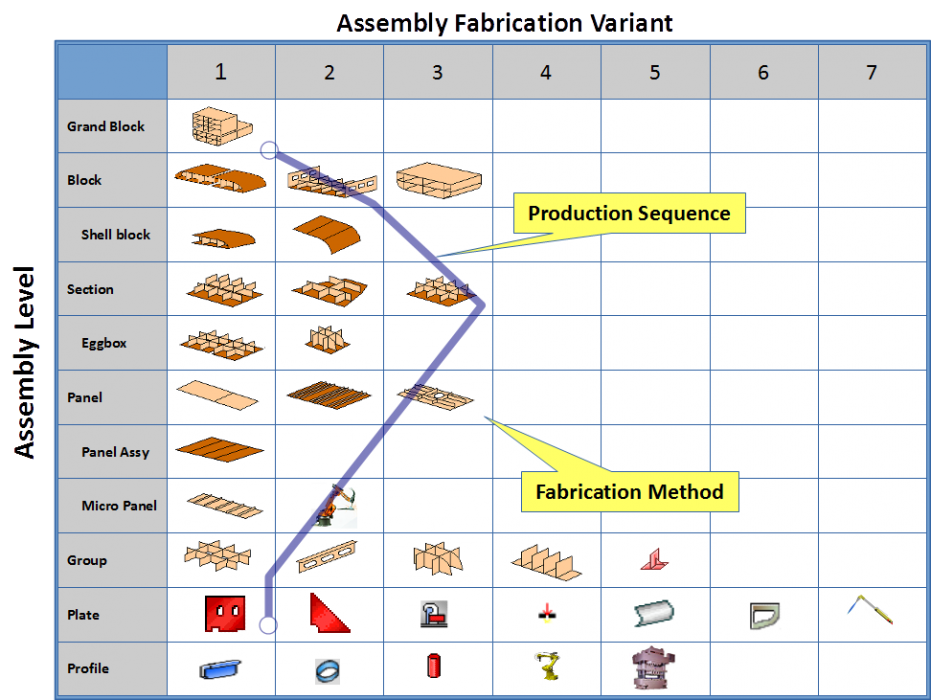
Production process steps are specified using a Fabrication Matrix, which links production stages to available production facilities. Each of the matrix cells represents a unique fabrication method to carry out the work at this production level. A Fabrication Method allows the user to define any number of rules describing the distortion effects occurring. Rules can be established from measured data, formula including stochastics, tabular data or heuristics and can furthermore consider other influences such as mounting sequences, welding technologies or weld sequencing. It is possible to define all available Fabrication Variants, each of them exposing specific distortion effects related to the technology applied.
As the product moves through production at different stages, the distortion effects will accumulate. This is accounted for by associating a fabrication sequence with parts and interim products. It allows to determine the impact of distortion based on actual production flows.
Capabilities
- Fully configurable distortion control: the configuration uses an intuitive model describing the production capabilities and related distortion effects, offering a considerable collection of parameters related to production equipment, production methods as well as part or assembly specific properties.
- Support for multiple sites: the system can be configured for any number of different production sites, which usually have different quality compliance characteristics. Each site will be model by means of a production facilities profile, which is captured in a corresponding fabrication matrix.
- of quality control feedback data (measurements, externally determined correction parameters)to continously update the system configuration
- Automated accuracy control for hull structure production embedded in the production preparation workflow: the solution fits seamlessly in the production preparation work flows, utilizing design data and production planning data as input and providing final part production geometry to be used for part nesting.
- Rule-based prediction of thermal deformation based on actual production sequence and methods used: using the configuration data, the identied production sequence is used to predict the deformation resulting from each production step and is accumulated to a total expected distortion at part level.
- Automated modification of part geometry: using the expected distortion for parts, a corresponding modification of part geometry is automatically applied, resulting in a new production geometry for parts affected by distortion.
- Just in time operation: as the distortion effects can be determined in a short period of time, part geometry modification can be applied in a just-in-time mode, allowing for last minute changes of production sequences or even switching production sites, should this be necessary e.g due to capacity constraints.
- Supports automated work breakdown structure (WBS) generation based on part/assembly properties and production capabilities: in shipyards where no such information is available during production preparation tasks, automated tasks can be executed by the system to identify the production sequences for any part or assembly
- Report generation: for each production step and production sequence, reports can be generated to provide information about the geometric modifications, the expected distortion effects and the resulting part or assembly dimensions. Such information is useful e.g. for verification during production.
Solution Components
The WDM solution includes:
- Topgallant® Facility Modeler application is main configuration tool to setup up the WDM system. Using this application, the shipyard production capabilities are modelled resulting in the setup of the custom Fabrication Matrix. QA Desktop is also used to update the rule sets based on the observed distortion effects.
- Topgallant® Assembly Production application with Distortion Management optionis the central application to select the production environment, target ship design and production data, to determine the total production effects and to process and update the part geometry.
- Topgallant® WDM Control Panel is provided to allow fully automated operation of WDM with minimal attendance through the execution of separate jobs that operate on a complete block or similar larger composition of parts of a ship.
- CAD/CAM publishing adapters provide a close integration with the available systems used to generate design and production data.
- Topgallant® Information Server is the lightweight, multi-user data management component that implements Atlantec-es' Enterprise Reference Model (ERM) for Shipbuilding, offering a large collection of engineering and organization business objects.
It supports complex data transformation tasks and process control requirements through a rich set of features like versioning, dependency analysis, and event tracking.
It is also capable of handling the large amounts of data typically found in shipbuilding environments. Topgallant Information Server supports a variety of common platforms. It is easy to set up and maintain using the included administration tool.
Customization

Topgallant solutions are prepared for flexible customization. Many items in the system can be configured by the user or system administrator.
Should there be a need for more customization such as integration of specialized systems, additional functionality demands, customization support is available to provide such additional features. Using the Topgallant infrastructure, we are able to provide this in a cost effective way.
WDM can be customized in many ways. For example, CAD geometry import can be tailored to the CAD data sources available. This can even be a mixture of different formats, e.g. when different parts of a ship design are sub-contracted to engineering services using different CAD tools.
Export of modified geometry can customized as well to match the individual production support software requirements for a shipyard.