Assembly Production
Assembly Production is an interactive application to manage production assemblies and the related process structure, often referred to as Work Breakdown Structure (WBS). It can handle products to be produced in one or
more shipyards or production sites. It is a modular application that consists of an assembly management platform and several modules that can be configured according to the user's needs.
The platform provides all the base functionality to review and modify assembly structures. In addition, the following plug-in modules are available:
- Assembly Definition: create and modify assemblies and their properties. This includes automated, rule-based definition of a complete WBS
- Task Sequencing: analyse production requirements to generate a production sequence.
- Distortion Management: analyze distortion effects due to assembly production processes and apply compensation results to affected parts
- Work Content Calculation: determine required production tasks and their work content
Assemblies typically reflect at least three aspects of production:
- a representation of the physical interim or intermediate result of a production stage, i.e. the assembled structure.
- a specification of the parts list defining the material requirements of the assembly interim product
- a description of the assembly process, defining required tasks or activities including their work content, schedule, resource requirements and other process parameters or constraints
Assemblies are by their nature establishing a hierarchy, which ultimately results in a completed product as its
top-level (or root) node, while the leaf nodes in a fully defined assembly tree are occupied by the individual lowest level constituents like parts, equipment items or similar.
Assembly structures in Assembly Production may originate in external systems. Using appropriate CAD, ERP, or Planing system data adapters, any predefined assembly structure can be retrieved for further processing.
Assembly Production Platform
The platform of Assembly Production provides all functionality to inspect, review and modify assembly hierarchies representing the complete or parts of the production hierarchy of a product. Access to all attributes is provided which enables the user to navigate and inspect down to the detail. Derived information such as actual dimensions, mass and geometric extent is calculated on demand.
Reviewing Assembly Information
For any existing or created assembly structure functions are provided to review the structure in detail. This includes the definition of the Assembly nodes themselves, as well as their part list information, and any information created or generated while working with Assembly Production.
Reviewing Part Information
Although Assembly Production does not manipulate parts or design structures as such, it is possible to review this data at any time. This includes all the properties of parts known to the system, including geometry data, if available.
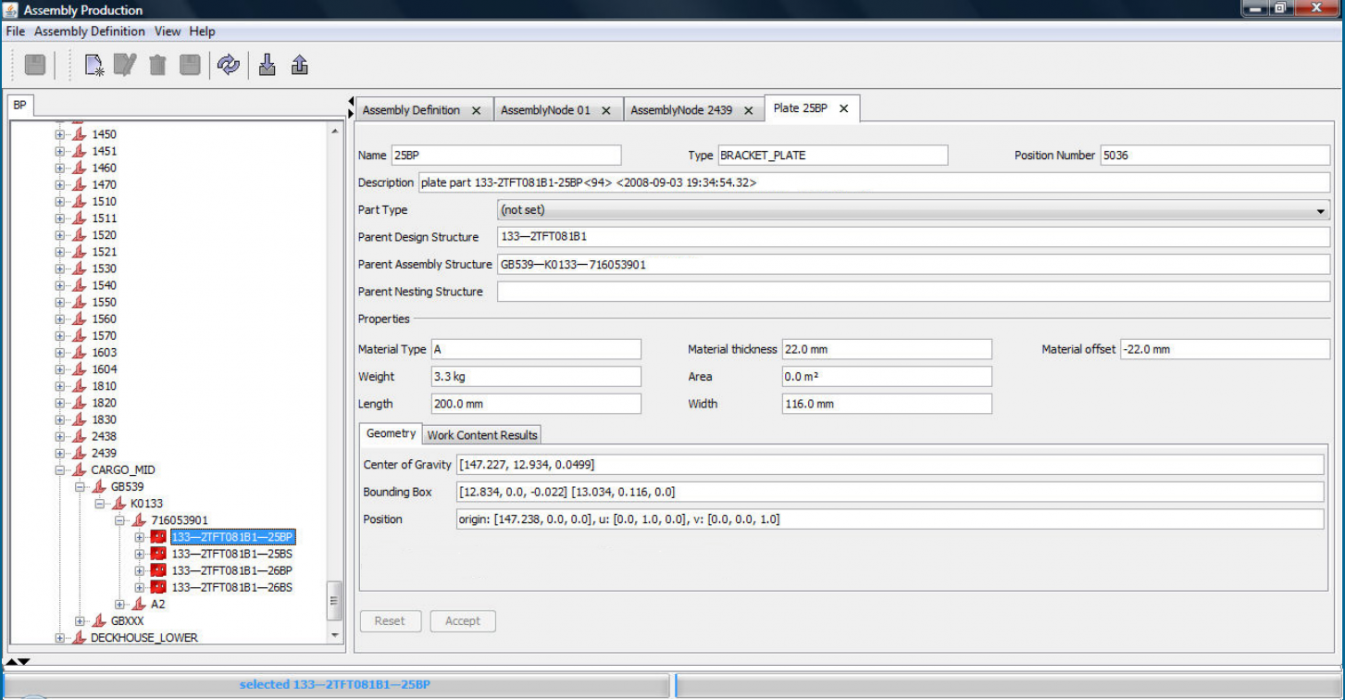
Visualization
This helpful capability allows to review the geometry of parts, design structures, and, most importantly, assemblies. The geometric representation is created from the underlying part geometry information and produces an impression of the interim product resulting from the execution of assembly processes up to the selected assembly node.
Report Generation
Assembly Production offers various reports to produce printed and list-type information based on the assembly structure and part data. For example, a predefined report generates the classic part list information for an assembly.
Assembly Definition
Using the Assembly Definition plug-in, assembly structures can also be build up from scratch. This is of interest in cases where no equivalent external system functionality is available or the design or planing processes have not advanced far enough. (Due to the version capabilities upgrading to external data becoming available later is always possible.)
Interactive Operation
This mode of operation is useful to perform additions, modifications or corrections to existing assembly structures. The user has full control over each step and all attributes being assigned.
Building up assemblies can be driven by part or design structure information, if this is available. In many situations, groups of parts or complete design structures will be included in a single assembly. Therefore, handy functions exist to support this grouping assignment activity based on the design structure.
It is also possible to create larger parts of the hierarchy by means of semi-automatic generation functions, which enable bulk data generation for regular structures.
Automatic Operation
The most powerful feature of Assembly Definition is the rule-based automatic generation of assembly structures based on existing design data. The function is controlled by a decision table system which can evaluate a wide range of properties to determine the target assembly structure. If desired, this function can include assignment of suitable fabrication methods.
Task Sequencing
Task sequencing is not always mandatory information required by ship production units. In many production environments, the actual detailled execution of production tasks is left to experienced production staff. However, to an increasing degree, having a well defined task sequence information is useful e.g. to carry out more precise estimation of work content and to carry out production simulation or scheduling tasks.
This need is addressed by the Task Sequencing plug-in of Assembly Production.
Within each assembly, the order of actual execution of production tasks depends on numerous factors. A lot of experience is often necessary to determine the best way to produce an assembly from its list of parts and sub-assemblies.
However, in quite a range of cases assembly structures follow patterns which can be analysed and used for general definition of task sequencing as part of an automated process.
The Task Definition plug-in allows the definition of task sequences either interactively or by using a automated calculation based on user-configurable rules.
The general idea is to use to the automated method to cover a large part of the task sequencing activity, allowing the user to focus on interactive refinement of the remaining special cases.
Distortion Management
The Distortion Management plug-in supports the analysis of production effects on part /assembly distortion, primarily due to heat introduced by welding and cutting processes.
The Distortion Management analysis operates on the basis of a shipyard/production site-specific set of distortion rules. The model for distortion analysis requires information about the production site capabilities and their expected distortion effects.
Once an assembly is defined, it can be assigned to a production site and a target fabrication method. At the user's choice, this can also be done via an automatic search for the applicable production methods of a site.
A fabrication method carries a set of site-specific distortion rules, which define shrinkage/distortion effects in a parametric form and which are used to determine how distortion will affect an assembly when produced using this method.
The combined effects of all assembly stages will ultimately be applied to the individual parts, resulting in a corresponding geometric correction, that considers the as-to-be-build conditions. This method can be applied in a just-in-time fashion, allowing for last minute changes of part geometry, assembly sequence or structure as well as rescheduling of production to other work places or facilities.
It is important to note, that this approach allows continuous updating so that e.g. changes in the methodology, update of equipment, or observed changes due to quality control measurements can be fed back into the process.
Work Content Calculation
The Work Content Calculation plug-in provides capabilities to assess the work content of an assembly and its related production processes. Assembly processes typically involve tasks like:
- Setup
- Fitting
- Welding
- Straightening
- Pre-outfitting
- Blasting
- Painting
- Insulation
- etc.
Extracting Work Content Information
As with most data in a Topgallant®, work content information may come as preexisting information from different sources like a planing system or ERP system. However, in many cases no or incomplete work content information exists.
To calculate work content, part and assembly properties may be used to estimate the amount work involved. Some of these properties may be fixed and known, while others may have to be calculated or estimated. For example, for painting operations, the area of all parts in a assembly will most likely one of the important drivers. However, other factors might have a strong influence, like the orientation or accessibility of a surface.
To deal with this it is possible to define rules, how the effort and supply material consumption can be determined on a set of such key properties. These rules in turn will need other base data during their evaluation. Therefore, underlying incomplete information has to be enhanced and completed by means of estimation or data provided by the user.
Work Content Analysis Rules
The work content calculation is driven by shipyard specific analysis rules. For each assembly level, process task types can be defined that will identify the types of work that may occur on that level.
For each task type default rules can be defined, which will be overridden or enhanced by level-specific rules, as required.